
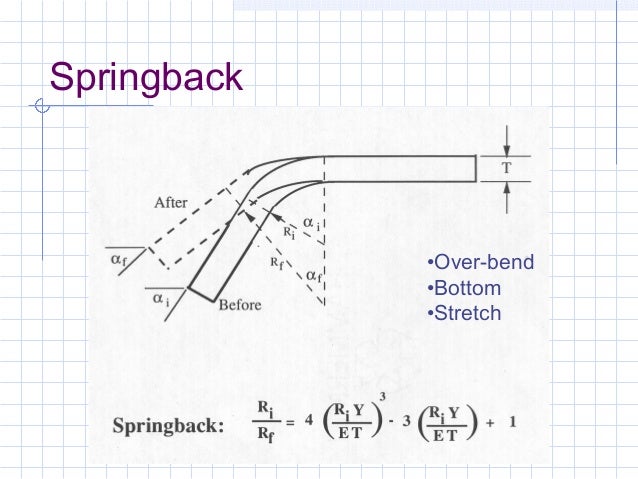
In coining, the entire face of the punch is stamped into the workpiece. It uses various punch angles along with a V die (see Figure 2). Bottom Bendingīottom bending forces the material around the punch nose. The punch nose produces the inside radius, which is used to establish the bend deduction. It requires dedicated, special tool sets for each bend and bend angle. Coining forces the entire tool profile to less than the material thickness, and thins the material at the point of bend. This method not only requires excessive tonnages, it also destroys the material’s integrity. Technically, any radii may be coined, but traditionally coining has been used to establish a dead-sharp bend. Coining forces the punch nose into the material, penetrating the neutral axis (see Figure 1). Unlike bottoming, coining actually penetrates and thins the material.Ĭoining is the oldest method and, for the most part, is no longer practiced because of the extreme tonnages it requires. Bottom bending and coining often are confused for the same process, but they are not. Note that there are three bending methods, not two. How exactly is this inside bend radius achieved? To uncover this, we must first look at the different methods of bending on a press brake: air forming, bottom bending, and coining. But to make this happen, you need to make sure every factor in the equation is what it should be, and this includes the inside bend radius. (Metal thickness exaggerated for illustration purposes.)īend allowances, outside setbacks, bend deductions-if you can calculate all of these with precision, you have a much better chance of bending a good part on the first try. The punch radius equals the resulting inside bend radius in the part. Figure 1: In coining, the punch nose penetrates the neutral axis of the material thickness.
